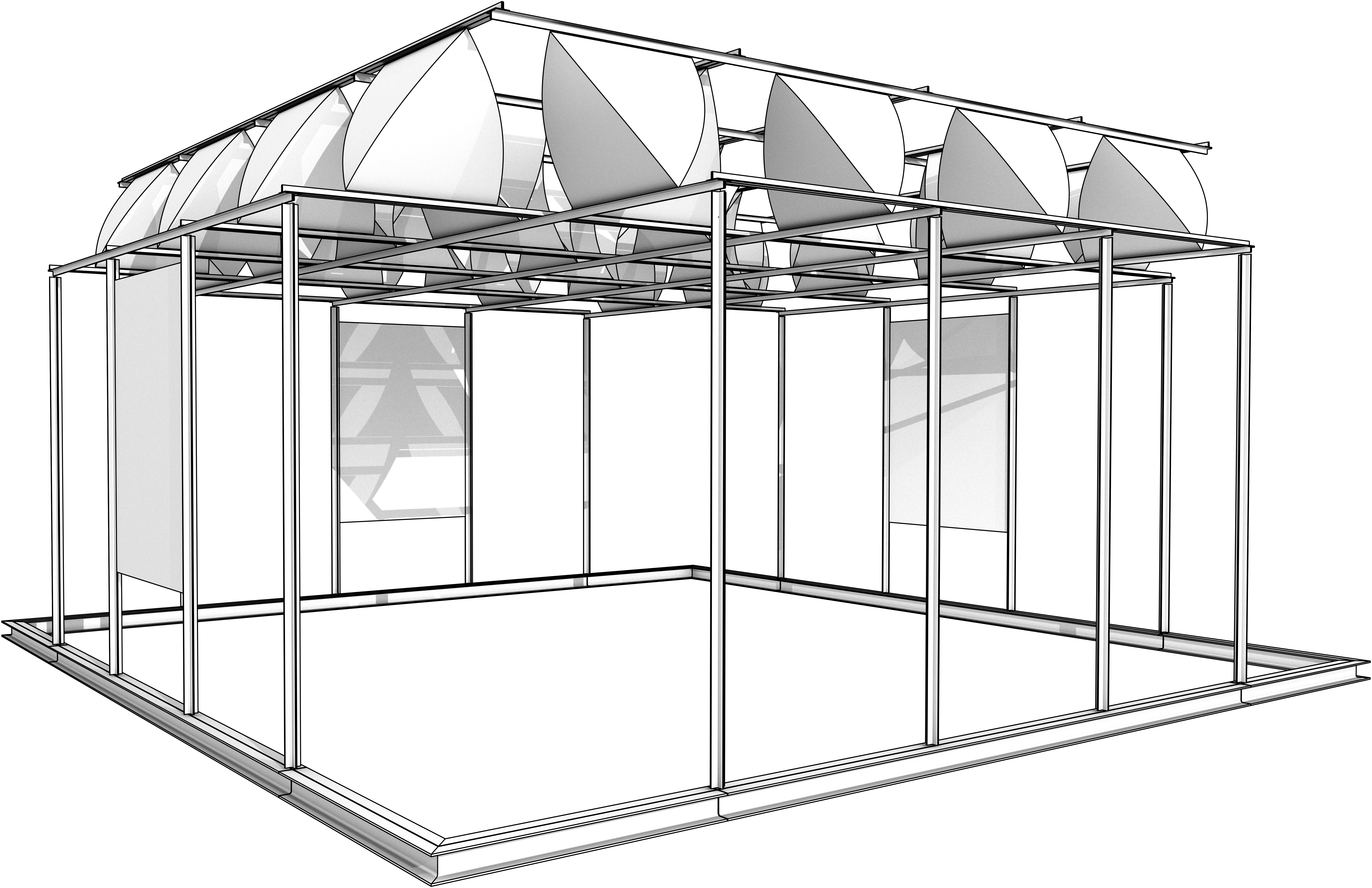
@ENPC – March. 2021 – N. Leduc
The classical double layer space truss is revisited by replacing diagonals with curved thin-walled polyhedral modules. The expected improvements are both technological and mechanical. The complex 8-branch nodes are broken down into a connection of two overlapping continuous members and a line connection between bars and the polyhedron edges. Curvature in the faces and edges of the modules introduces shape resistance whilst stabilizing the members against buckling.
Facts and figures
- Dimensions: 6 x 6 x 0.7 m
- Weight: 800 kg
- Total vertical load: 24 kN
- Maximum deflection: 3.8 mm
- Number of fixing points: 2198 u
- Time to assemble: 4 days x 4 people
- Material: galvanized steel
- PhD Student: N. Leduc
- Laboratoire Navier: C. Douthe, O. Baverel
- Université Grenoble-Alpes: G. Hivin
- TESS: S. Aubry, B. Vaudeville
- Viry: K. Leempoels
Description of design strategy
The prototype developed here is based on the semi-regular tessellation of space, consisting of a concatenation of tetrahedra and octahedra. The latter are truncated to become square-based pyramids with apex oriented alternately upwards or downwards.

To determine the final shape of the modules, each tetrahedron is parameterised by a set of variables that control the height, length, width and geometry of the edge curves. A constrained optimization is then carried out with the dual objective of improving mechanical behaviour (maximization of the buckling load factor) and reducing the quantity of material (minimization of the surface area of the tetrahedrons).
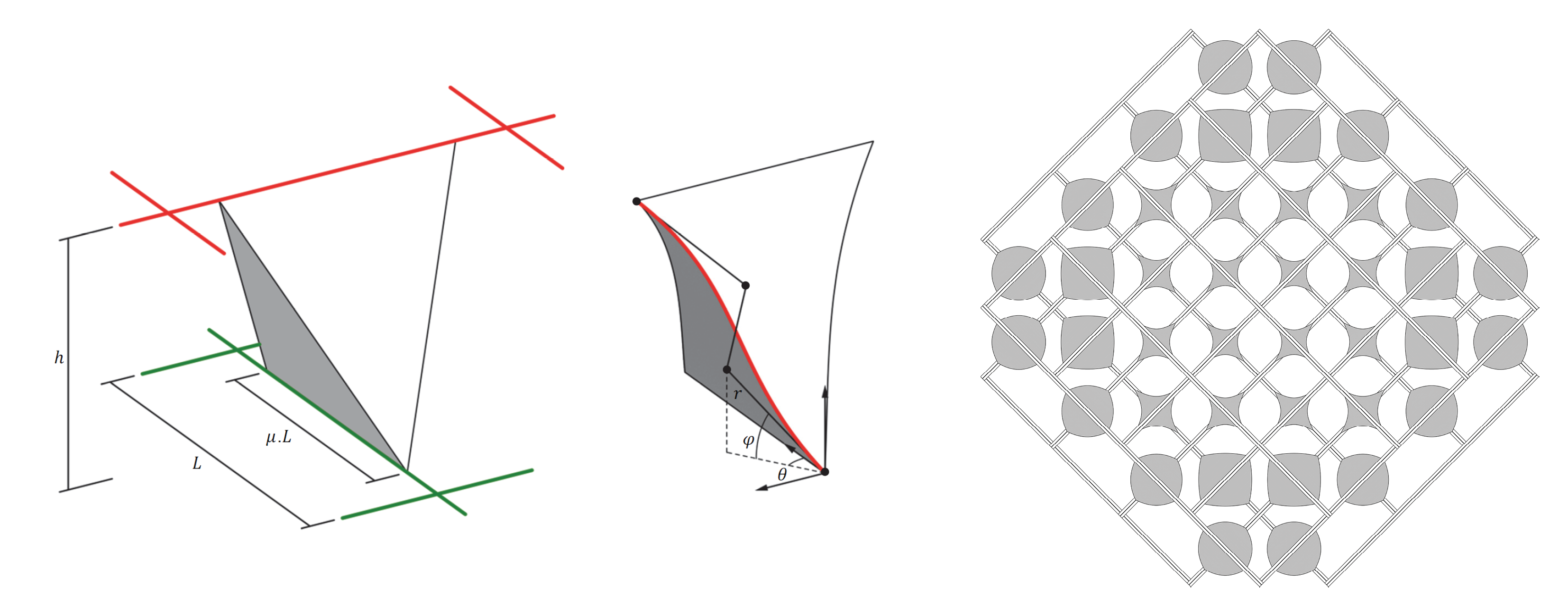
Developpable sheet assembly sequence
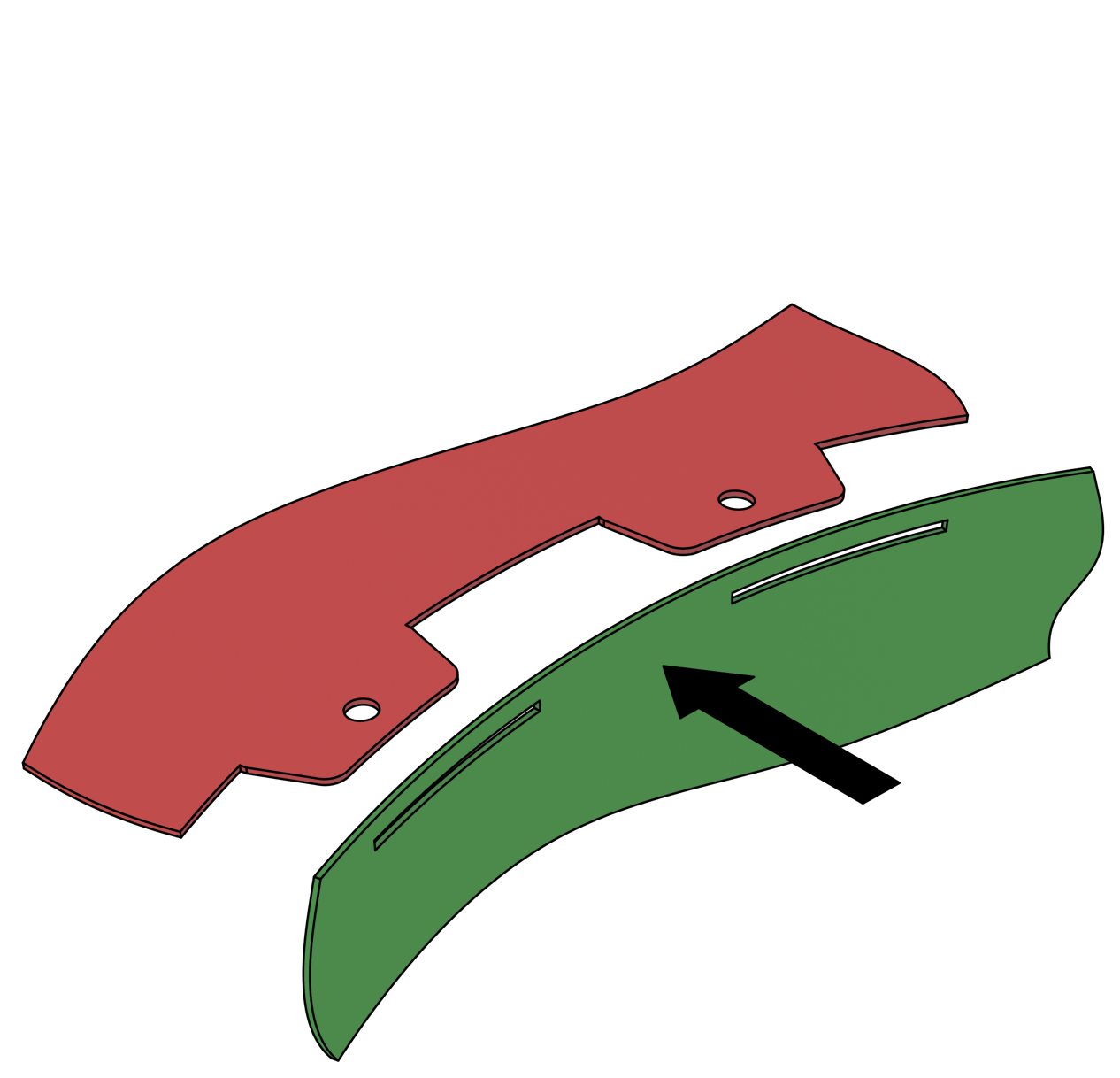
Complete structure assembly sequence
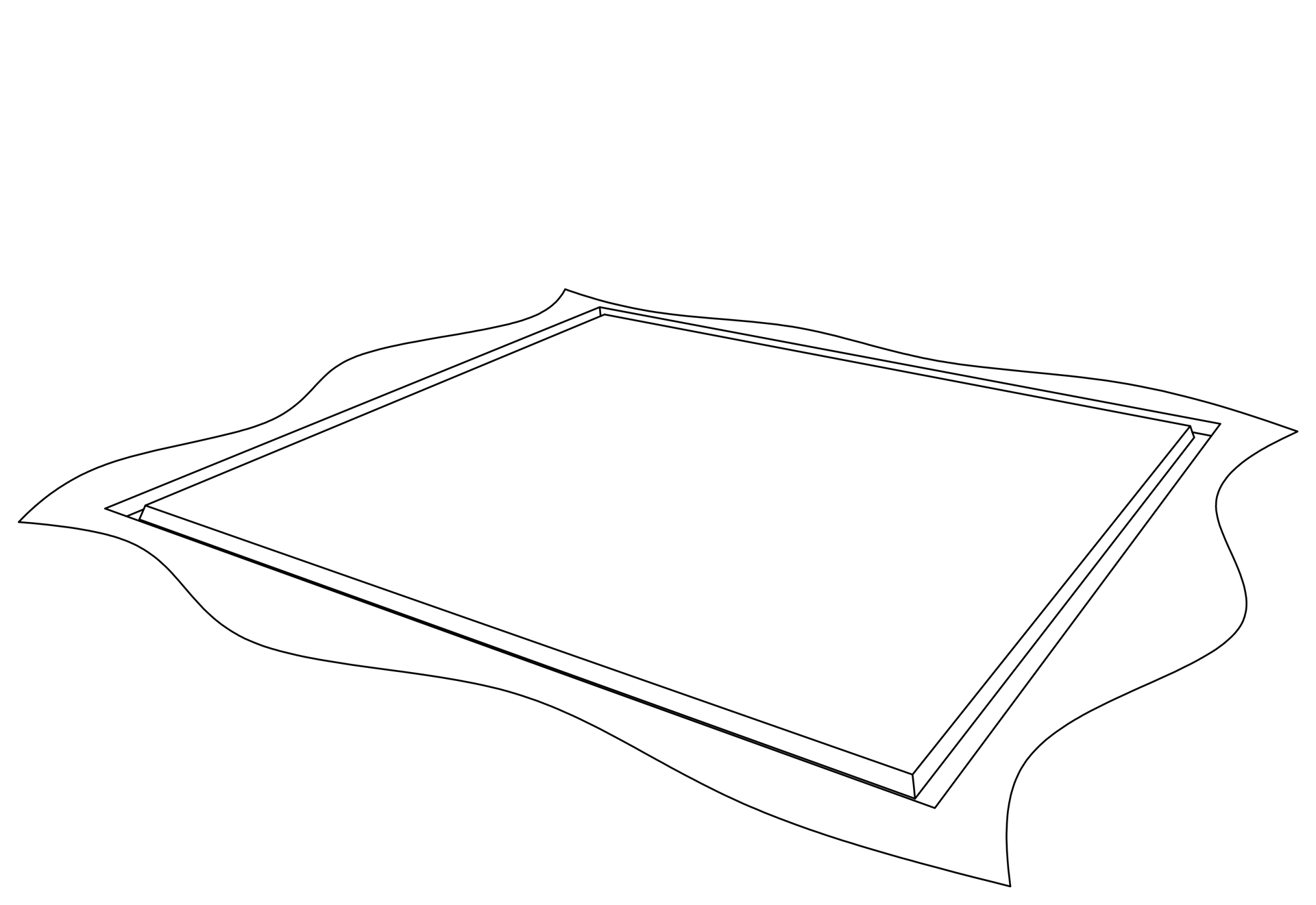
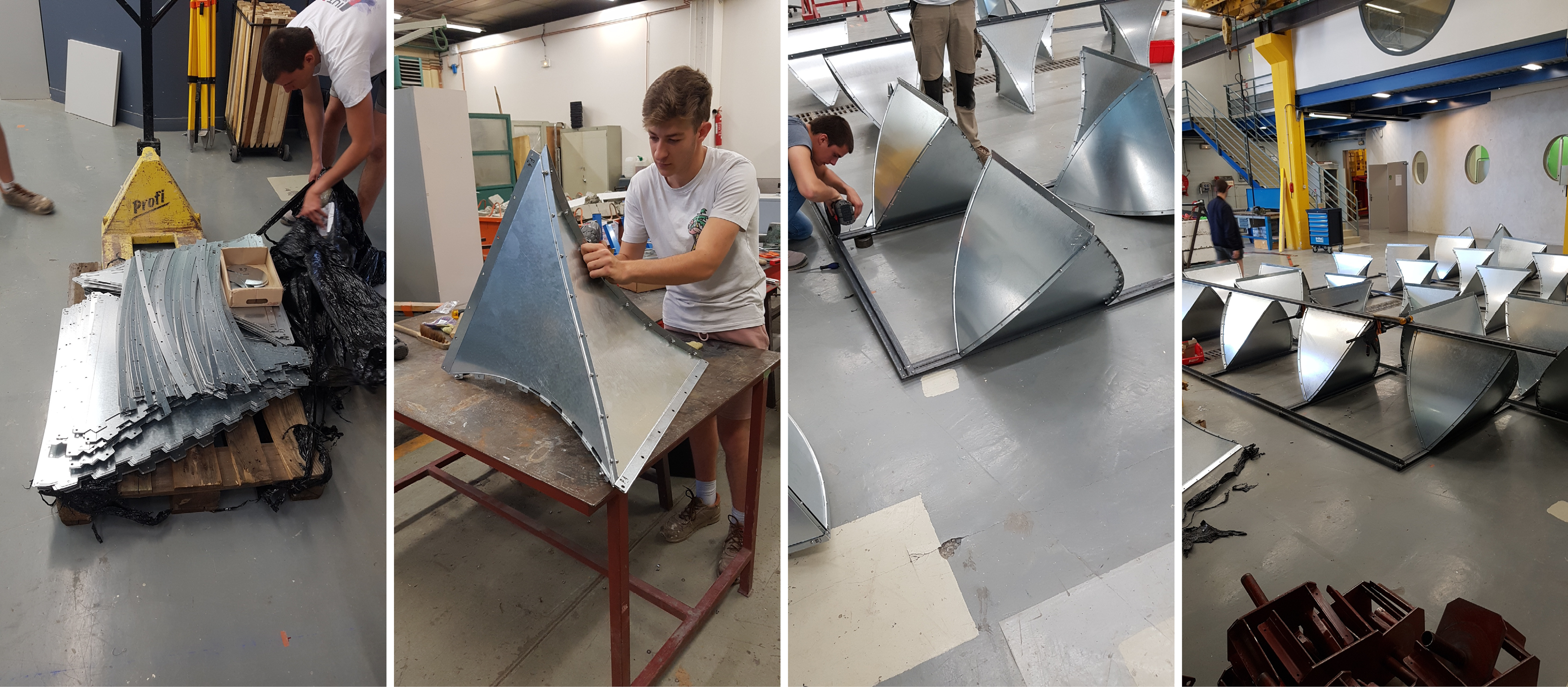
Relevant references
Leduc, N., C. Douthe, G. Hivin, B. Vaudeville, S. Aubry, K. Leempoels, and O. Baverel (2019). Space Structure with Developable Shear Components. In Proceedings of the International fib Symposium on Conceptual Design of Structures, Spain, pp. 345–352.