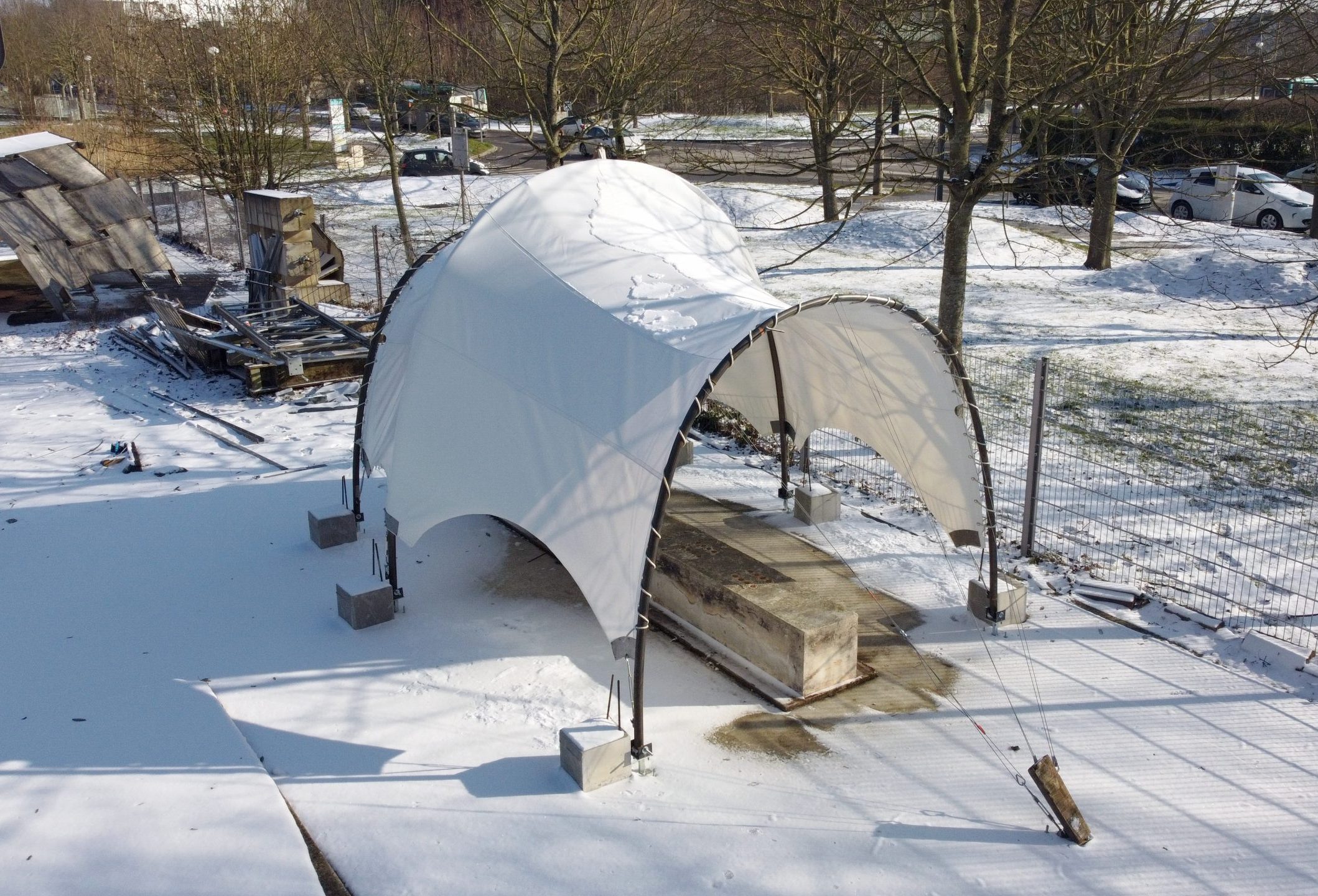
@ENPC – March. 2021 – K. Wallia
FAB Shell is a demonstrator showcasing the feasibility of building thin anticlastic concrete shells using tensile membrane and telescopic arches as a formwork. After the concrete is sprayed over the membrane and set, it is possible to remove the entire formwork and reuse it in future for building a shell of same scale and size. The key aspects were to determine the structural efficient form using computational methods and showcase actual fabrication of the novel formwork technique. Fabric is light in weight and takes comparatively lesser time during confection and to put in form. The telescopic arches can be retracted easily underneath the set concrete shell and can also be reused multiple times.
Facts and figures
- Dimension: 3.25m span x 4m long x 2.7m high
- Material Used: 50mm dia Steel Pipe Arches, PVC Coated Flexible Composite SF 905F3, Steel Cable
- Surface Area: 20sq.m
- Total Weight of Prototype: 62kgs
- Assembly Time: 8 hours x 6 people
- Anticipated Shell Thickness: 2.0 cm
- Student: Krittika WALIA, Design by Data, ENPC
- Advisors: Olivier BAVEREL (Ecole des Ponts ParisTech), Robin OVAL (University of Cambridge)
- Laboratorie Navier: Jean-Francois CARON, Hocine DELMI
- Dynamophe: Felix CHAMEROY
- Würth France: Stephen CONCORD
Description of design strategy
Dynamic Relaxation (Barnes et al, 1999) has been opted as a form-finding strategy using Kangaroo plugin (Piker et al, 2013) for Grasshopper. The workflow comprises of three stages of construction with corresponding finite element analysis using Karamba3D (Preisinger et al, 2014):
- formwork assembly,
- spraying of concrete, and
- final shell after formwork removal.
The three stages simultaneously informed the shape of the membrane and the arches. The membrane was targeted to be in pure tensile state at Stage 1. Then, concrete load was added sequentially and membrane’s behaviour was analyzed at each step. At Stage 3, the concrete shell was targeted to act majorly in compression under different loading cases.
Detailing
After achieving the final form post analysis, developable surfaces were extracted and unrolled, and membrane confection was carried at Dynamorphe. Each arch was made in three parts, where the top-middle is retractable, hence enabling easy disassembly and uses basic nut-bolt joinery for blocking the sliding movement.
Relevant references
R. Barnes, “Form finding and analysis of tension structures by dynamic relaxation,” Int. J. Sp. Struct., vol. 14, no. 2, pp. 89–104, 1999, doi: 10.1260/0266351991494722.
Daniel piker, “Kangaroo: Form Finding with Computational Physics,” 10.1002/ad.1569, 2013.
H. Clemens Preisinger, “Karamba—A Toolkit for Parametric Structural Design,” Link. Struct. Parametr. Geom. Archit. Des., vol. DOI: 10.10, no. 83, pp. 110–113, 2014.