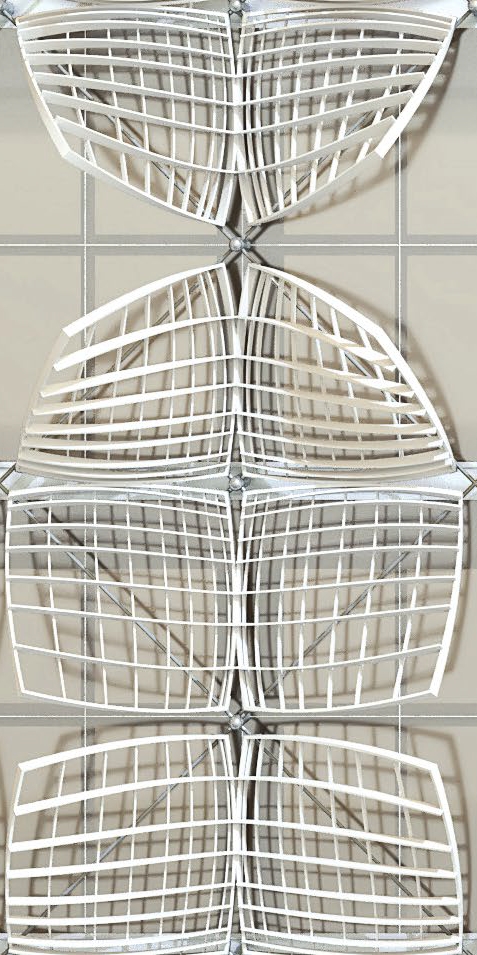
Advances in Architectural Geometry 2020
Conference on-line library
The Advances in Architectural Geometry (AAG) conferences are a unique forum where developments in the design, analysis and fabrication of building geometry are presented. With participation of academics and professionals, each conference aims to gather and present practical work and theoretical research that responds to contemporary design challenges and expands the opportunities for architectural forms.
The seventh edition of the AAG conferences was hosted by Ecole des Ponts ParisTech, Université Gustave Eiffel and Navier laboratory, France in April 2021, 28-29.
27 pier-reviewed papers have been selected by the scientific committee and divided into long and short presentations. Detailed abstracts can be found hereafter, as well as links to full papers and presentation videos. Note that the paper version of the proceedings has been published by Presses des Ponts.
Papers selected for long presentations
Sessions chaired by Mark Pauly Wednesday April 28, 2021
Architectural Free-form Surfaces Designed for Cost-effective Panelling Through Mould Re-use – Pellis et al.
Authors
D. Pellis, M. Kilian, H. Wang, C. Jiang, C. Müller, H. Pottmann
Abstract
The realization of architectural free-form skins is a big challenge, in particular if one desires a smooth appearance and uses curved panels. These have to be brought into shape by special manufacturing technologies, most of which require the costly production of moulds. Previous approaches to mould re-use relied on optimization algorithms which play with the available tolerances and allowed deviations from the reference geometry. One aims at a good trade-off between fabrication cost and a visual appearance which comes close to the original design intent.
For general free-form surfaces, there may be no other ways to computationally solve the panelling problem. However, we will show in this paper that there is a rich class of surfaces which very much look like free-form shapes, but have significant advantages over totally unrestricted free-form geometries. These surfaces are known as Weingarten surfaces. They are characterised by a relation between their principal curvatures, leading to a just one-parametric family of curvature elements and thus local surface shapes. This allows one to fabricate N panels with a number of moulds which is roughly just √N. Moreover, if the panels are fabricated from material which is not rigid after panel production, one can exploit the allowed deformations through bending and further increase the accessible shape variety or reduce the number of moulds even more. We also provide an overview of computational techniques for the computation of Weingarten surfaces and their deformation through bending and illustrate the approach through a number of architectural case studies.
Form-Finding with Isotropic Linear Weingarten Surfaces – Tellier et al
Authors
X. Tellier, C. Douthe, L. Hauswirth, O. Baverel
Abstract
Isotropic Linear-Weingarten surfaces are a rich family of shapes, which contains some popular architectural surfaces such as paraboloids. We prove that these shapes are funicular for a uniform vertical load, and that the stress lines then form a conjugate net. This allows to design structures with planar facets, in which the edges have an optimal mechanical orientation. We introduce a generation method based on iterative projections. The method allows to intuitively control the shape by its boundaries and two design parameters. The formal potential is demonstrated on several examples.
Computational Design and Optimisation of Quad Meshes Based on Diagonal Meshes – Jiang et al
Authors
C. Jiang, C. Wang, E. Schling, H. Pottmann
Abstract
A significant amount of research in Architectural Geometry has dealt with skins and structures which follow a quadrilateral layout with double curvature. In many cases, such quad networks are computationally accessed by quad meshes which obey various constraints. These may concern planarity of faces, supporting structures which follow specific curvature paths, conditions on node angles, static equilibrium and others.
In this paper we draw the attention to a new way of computing such constrained quad meshes. The new methodology is based on the diagonal meshes of a quad mesh and the checkerboard pattern of parallelograms one obtains by subdividing a quad mesh at its edge midpoints. The new approach is easy to understand and implement. It simplifies the transfer from the familiar theory of smooth surfaces to the discrete setting of quad meshes. This is illustrated with planar quad meshes and asymptotic nets, in particular with those exhibiting a constant node angle.
The application of such networks has advanced fabrication-aware-design in the architectural practice. Looking at asymptotic nets specifically, we list their potentials and challenges for the construction of strained gridshells. The benefits of constant node angles are highlighted along different construction methods in timber and steel. We conclude with current developments, looking at less-restricted and transformable asymptotic structures, and how they are designed.
Sessions chaired by Laurent Hauswirth, Wednesday April 28, 2021
Discretised Airy Stress Functions and Body Forces – Chiang et al
Authors
Y.-C. Chiang, P.J. Buskermolen, A. Borgart
Abstract
This paper extends polyhedral Airy stress functions to incorporate body forces. Stresses of an equilibrium state of a 2D structure can be represented by the second derivatives of a smooth Airy stress function and the integrals of body forces. In the absence of body forces, a smooth Airy stress function can be discretised into a polyhedron as the corresponding structure is discretised into a truss. The difference in slope across a creases represents the axial force on the bar, while the zero curvatures of the planar faces represent zero stresses voids of the structure. When body forces are present, the zero-stress condition requires the discretised Airy stress function to curve with the integrals of these body forces. Meanwhile, the isotropic angles on the creases still indicate concentrated axial forces. This paper discretises the integrals of body forces into step-wise functions, and discretises the Airy stress function into quadric faces connected by curved creases. The proposed method could provide structural designers (e.g. architects, structural engineers) with a more intuitive way to perceive stress fields.
Tensioned Principle Curvature Cable Nets on Minimal Surfaces – Sehlstrom et al
Authors
A. Sehlström, C. J. K. Williams
Abstract
Cable nets are efficient and elegant structures that are pre-stressed to limit their deflection under loading. The best known cable net structure is the Munich Olympia stadium built for the Olympic games in 1972 by Frei Otto and Jörg Schlaich. Frei Otto believed that the ideal shape for such structures is a minimal surface with uniform surface tension under pre-stress. However, a minimal surface can only be approximated by the equal mesh nets used by Frei Otto, but it is possible to produce a true pre-tensioned minimal surface with a fine net of cables forming a pattern of curvilinear squares, which includes a net following the principal curvatures of the surface. Both an analytical and a numerical approach for the form-finding of minimal surfaces with a principal curvature net are described. The analytic approach uses the fact that every minimal surface with principal curvature coordinates can be expressed by a single function of a complex variable. This is a special case of the Weierstrass–Enneper parametrisation which uses two functions, but one of them effectively only controls the pattern of coordinates on the surface. The numerical approach automatically produces a minimal surface and the principal curvature coordinates at the same time and can be applied to any minimal surface whose boundaries are either principal curvature or asymptotic directions, or a combination of the two. Straight lines and cable boundaries form asymptotic lines and a surface which is normal to a sphere has a principal curvature direction as its boundary.
Kinetics and Design of Semi-Compliant Grid Mechanisms – Schikore et al
Authors
J. Schikore, E. Schling, T. Oberbichler, A. M. Bauer
Abstract
The research of transformable structures has fascinated architects, engineers, and mathematicians (e.g. Piniero, Hoberman, Otto, Finsterwalder). Their potential to adapt to environmental conditions and user’s needs or to aid the erection process has produced beautiful and complex designs (e.g. Hoberman sphere, Multihalle Mannheim). We can distinguish between conventional, discrete rigid-bodymechanisms and so-called compliant mechanisms, which utilise the elasticity of members to perform controlled elastic deformations (Howell 2001). Recent developments in elastic gridshell construction have used this kinetic behaviour for the construction process and transformation (X-Shells, G-Shells, Asymptotic Gridshells).
This paper aims to unravel the categories of such kinetic gridshells, and presents fundamental principles of semi-compliant quadrilateral grid structures with uniaxial rotational (scissor) joints built from initially straight, continuous beams. We use specific lamella profiles that restrict the elastic deformability, disabling at least one of the three local bending axes. Depending on the orientation of the profiles, we can categorise three families – doubly ruled (straight), geodesic and asymptotic networks – each exhibiting distinct kinetic properties with limited degrees of freedom. We verify our theory using a matrix of 3 x 2 basic/fundamental grid configurations. By controlling the structure’s parameters, we can design their shape and behaviour. Introducing the curvature-square diagram further allows us to understand and predict their kinetic performance. We present architectural applications of both experimental and built structures and apply our theory to a novel design for the kinetic umbrella, a transformable asymptotic gridshell.
Sessions chaired by Helmut Pottman, Wednesday April 28, 2021
Curved Crease Edge Rounding of Polyhedral Surfaces – Maleczek et al
Authors
R. Maleczek, K. Mundilova, T. Tachi
Abstract
We show a novel method to design a curved crease folding that constructs the edgerounded, i.e., filleted, version of a given polyhedral surface. We replace each edge with a smoothly rounded cylinder and each vertex with a generalised cone, such that the surfaces joined through curved creases form a single developable surface with possible cuts at the singular cone apices. Because the curved crease can be explicitly computed from the isometry of corresponding line segments for given locations of the cone apex in 2D and 3D, our problem reduces to identifying the locations of the apices. We characterise the conditions for the apex positions and provide a numerical scheme to find the apices for the given mesh by solving a nonlinear optimisation problem. In general, the rounding of edges reduces the surface area, so the resulting curved folded surface is not isometric to the original polyhedron; in particular, the surface is not guaranteed to be foldable from a single piece of uncut paper if applied to a developable polyhedral surface. We solve this problem by computing consistent material loss caused by rounding radii.
Flat-Foldable Rigid Origami with Uniform-Thickness Panels – Shimoda et al
Authors
Y. Shimoda, T. Tachi, J. Sato
Abstract
In this paper, we present a novel design method of rigidly foldable origami composed of panels with uniform thicknesses. Our design is based on quadrilateraltransformable mesh composed of degree-4 vertex with equal opposite sector angles, forming a family of corrugated surfaces that folds flat. We apply thickness to such a rigidly foldable surface by extending the axis-shift method to degree-4 vertex with equal opposite angles. Using our method, each panel ends up having uniform thickness.
We investigate the necessary and sufficient conditions on the pair of opposite angles and the thickness ratio for each saddle-like vertex to maintain the kinematics after thicknesses were applied. We construct parametric design models based on the derived constraints and explore the design space. The design examples of transformable structures are potentially applicable to architectural design. The resulting structures efficiently fold up to completely flat states with 180° fold angles, wherein the total thickness is the sum of the thicknesses of overlapping panels. This also allows for fabrication by first cutting out each panel and subsequently assembling them in the flat-folded state.
Curved-crease Paperfolding Structures and their Tectonics – Koschitz
Authors
D. Koschitz
Abstract
Given the constraint of curved-crease paper folding, which type of sheet-structure with compliant hinges can be designed and fabricated? This paper investigates mirror reflections of developable surfaces for structures and provides the results of proof-of-concept prototypes that demonstrate how this specific topic in geometry can be used to create stiff surface structures. The specific method to create curved creases is based on mirror reflections of cylinders, cones and tangent surfaces, which can be constructed with CAD software. The goal of the presented case studies is to highlight design principles and tectonic solutions related to 2D manufacturing. This paper reports on projects such as a single surface shell, furniture designs, building parts and a double surface structure, all made of vulcanized fibre sheets. The material is made of polymerized cellulose and is available in large sheets. The material becomes malleable when it is wet, which enables the folding of compliant hinges. The findings of the built projects provide tectonic solutions that relate this topic in geometry to the logics of sheet assemblies.
Sessions chaired by Romain Mesnil, Wednesday April 28, 2021
Meshing with Kagome Singularities – Topology adjustment for representing weaves with double curvature – Ayres et al
Authors
P. Ayres, J. You-Wen, J. Young, A.G. Martin
Abstract
In this paper, we present a planar mesh topology adjustment scheme for the automated production of principled Kagome weave patterns.
Kagome is a triaxial weave system based on a hexagonal lattice. Double curvature is induced by replacing hexagonal cells with alternative polygons. These singularities are digitally represented by constructing a tri-mesh with appropriate valence. However, the automated adjustment of meshes remains an open challenge.
The topology adjustment scheme presented here employs edge flipping to modify a regular valence 6 mesh. A key insight is that embedding a local valence modification necessitates a cascade of edge flips that extend out to the mesh boundary.
We demonstrate the application of this principle to represent a range of singularity valences and verify these individually with simulation. A series of case studies demonstrate how: 1) the scheme can accommodate multiple singularities within a mesh; 2) the scheme can be integrated into a digital design pipeline that includes fabrication documentation production for producing physically woven Kagome approximations using only straight strips of material.
Within the paper, we contextualise this work with reference to the state-of-the-art, articulate its contribution, discuss the limits of the scheme and reflect upon its broader relevance to architectural design and construction.
TopoGAN Topology Optimization with Generative Adversarial Networks – Bernhard et al
Authors
M. Bernhard, R. Kakooee, P. Bedarf, B. Dillenburger
Abstract
Topology optimization (TO) is a numerical simulation to identify an optimal distribution of solid and void. A more efficient distribution of material means a reduction of natural resources consumption. TO results in branching structures, difficult to manufacture with conventional methods. Advances in additive manufacturing allow the production of components at an unforeseen level of complexity. The computational cost and the need for expert knowledge in setup prevent TO from being part of architects’ set of instruments. Data-driven artificial intelligence (AI) improved not only classification tasks but also spawned various synthetic models. We trained a generative adversarial network (GAN) with the boundary conditions as input and the result of a conventional TO as output. We chose a wall with randomly placed openings as a case study and produced three different training sets. The GAN was able to generate an output in a fraction of a second. The network learned to output structures close to the ground truth and generalized even across data sets. We measured the accuracy of the generated results with different metrics. The accuracy of the results was very encouraging within a few percents of the target value’s deviation. The significant speed improvement is a first and promising indicator of how machine learning could provide real-time feedback to the designer. Integrated into a CAD environment, dynamic updates, even for complex tasks, are invaluable in the conceptual design phase. Such an instrument can help the designer save material and most efficiently layout the building structure.
Biomimetic Generative Morphologies for 3D-Printing – Guerguis et al
Authors
M. Guerguis, S. Principe
Abstract
The recent development of computational form-finding and additive manufacturing (AM) has broadened the opportunity for extensive exploration into the design of highly-efficient structural systems. The research presented in this paper investigates the potential to which topology optimisation and AM can be used to extend the boundaries of the design of high-performance construction systems. The main objective of this research is developing computational design to digital fabrication workflow for the construction of robotically controlled 3d-printed building assemblies. The topology optimised structure was developed using a novel topology optimisation workflow. This process builds up material only in areas of high stress based on biomimetic principles found in nature, maximising structural performance while minimising weight. The inherent qualities of AM, such as its ability to create complex geometries with high levels of accuracy and construction automation, make it an ideally suited method to produce these prototypes. This paper includes the development of generative design methodologies for AM workflows. By implementing these robotically controlled AM processes at multiple scales, this work can have wide-reaching applications in the construction industry. This paper presents the overall research methodology with an emphasis on computational design, structural analysis, evaluation, and the fabrication of scale models prototypes.
Sessions chaired by Cyril Douthe, Thursday April 29, 2021
Filigree Shell Slabs – Christie et al
Authors
J.Christie, S. Bodea, J. Solly, A. Menges, J.Knippers
Abstract
In recent years, the coreless filament winding (CFW) technique has gained attraction due to its capacity to effectively realize large-scale lightweight building components out of fibre-reinforced composites. However, the sequential nature of its filamentbased production process imposes a series of design constraints that restrain the use of this technique in new typologies and applications. The current research introduces a novel shape optimisation-to-fabrication method that expands the scope of CFW towards the production of load-bearing components for slabs. A multi-stage workflow is proposed, integrating parametric design, shape optimisation, stress-driven material layup, and fabrication to ensure a high level of consistency between form and materialization. The research is presented in two phases. The first phase explores the use of shape optimisation to comprehend the underlying logic of shell forms capable of performing under the specific requirements of the slab scenario. The second phase integrates the inherent conditions of the material, formwork system, and robotic filament winding process into a seamless design-to-manufacturing workflow. The research resulted in a 10.2 kg prototype of a slab load-bearing structure that withstood a load of 559 kg while spanning 2.7 m, demonstrating the effectiveness of the approach.
Printing on Fabric Meta-Material for Self-Shaping Architectural Models – Jourdan et al
Authors
D. Jourdan, M. Skouras, E. Vouga, A. Bousseau
Abstract
We describe a new meta-material for fabricating lightweight architectural models, consisting of a tiled plastic star pattern layered over pre-stretched fabric, and an interactive system for computer-aided design of doubly-curved forms using this meta-material. 3D-printing plastic rods over pre-stretched fabric recently gained popularity as a low-cost fabrication technique for complex free-form shapes that automatically lift in space. Our key insight is to focus on rods arranged into repeating star patterns, with the dimensions (and hence physical properties) of the individual pattern elements varying over space. Our star-based meta-material on the one hand allows effective form-finding due to its low-dimensional design space, while on the other is flexible and powerful enough to express large-scale curvature variations. Users of our system design free-form shapes by adjusting the star pattern; our system then automatically simulates the complex physical coupling between the fabric and stars to translate the design edits into shape variations. We experimentally validate our system and demonstrate strong agreement between the simulated results and the final fabricated prototypes.
Sessions chaired by Mélina Skouras, Thursday April 29, 2021
Integrative Design Methods for Spatial Winding – Duque Estrada et al
Authors
R. Duque Estrada, F. Kannenberg, H.J. Wagner, M. Yablonina, A. Menges
Abstract
A cooperative multi-robot system was developed to leverage the fibre’s potential to act as formwork and allows to create wound filament connections which reduce the necessary formwork to a bare minimum. The developed process results in a novel typology of lightweight fibrous space frame structures. This paper contextualizes the presented work and introduces design methods for the developed spatial filament winding process. Syntax logics and rules were informed by geometric dependencies and fabrication-driven constraints. Computational design tools were developed to simulate the interdependent material behaviour and structurally inform the created artefacts. The proposed strategies and fabrication system expand the design possibilities of lightweight fibre structures and demonstrate the potentials of tailoring the fibres in space.
Redefining Polyhedral Space Through 3D Printing – Kladeftira et al
Authors
M. Kladeftira, M. Leschok, E.Skevaki, B. Dillenburger
Abstract
Space frames (SF) are perhaps the most used lightweight spatial structures in the construction sector. They are identified as a highly prefabricated and standardised construction system. However, as computational design brings forward more complex forms and freeform shapes, standardized modular systems are presenting difficulty to retro-fit complex forms.
Advances in Additive Manufacturing (AM) present opportunities to fabricate customized structural parts. More specifically, the fabrication of bespoke connections with AM bares great potential to overcome geometrical limitations in SF construction. Geometrical differentiations can be combined with functional integration at no extra cost. 3D printing offers the missing link to effectively establish a digital chain, from design to fabrication for non-standard SF.
This paper examines generative computational methods for creating case-specific, bespoke connections designed for AM. In combination with studies in density, topology, and materiality of the connections possibilities of new geometric space articulation, new aesthetics, and finally, multi-functional structural frames arise.
A series of case studies of bespoke SF design at different scales are reviewed and address a variety of functional nodes ranging from stiff axial connections to fully flexible spring ones. Finally, the paper critically discusses the geometrical benefits and limitations of the presented methods for digital bespoke space frames.
Sessions chaired by Bill Baker, Thursday April 29, 2021
Synthesis of Kit-of-parts Structures for Reuse – Bruetting et al
Authors
J. Brütting, G. Senatore, A. Muresan, I. Mirtsopoulos, C.Fivet
Abstract
This paper shows a computational workflow to design a kit of parts consisting of linear bars and spherical joints that can be employed to assemble, take apart, and rebuild diverse reticular structures, e.g. gridshells and space frames. Being able to reuse bars and joints among different structures designed with this method reduces the material demand compared to one-off construction. The input of the method is a set of different reticular structures intended to be built from a common kit of parts. In a first step, the structure geometries are optimised such that the structures share groups of members with identical lengths to allow the placement of same bars in all structures. In a second step, the kit-of-parts joints are optimised to allow their reuse in different structures as well. This is achieved by merging the specific connection patterns of nodes from different structures into one joint. The potential of the proposed method is demonstrated via its application to two case studies: 1) the design of three temporary space frame roofs, and 2) the realisation of three pavilion-scale prototypes serving as a proof of concept. The latter case study also shows the robotic fabrication of the bespoke joints.
LightVault: A Design and Robotic Fabrication Method for Complex Masonry Structures – Parascho et al
Authors
S. Parascho, I. X. Han, A. Beghini, M. Miki, S. Walker, E.P.G. Bruun, S. Adriaenssens
Abstract
This paper presents a novel approach to masonry construction: utilising cooperating robots to construct complex doubly-curved vault geometries while eliminating the need for false- or formwork. An integrated design method that was developed, which takes into account both robotic and structural constraints and includes the following steps: (1) the overall design volume is defined based on the robots’ position, reach, and collision constraints; (2) a form-finding approach using Airy’s stress function is used to generate the target geometry; (3) the geometry is tessellated into a herringbone brick pattern; (4) the robotic construction sequence is defined based on stability and reachability constraints.
Parallel to the development of the design methodology, the paper presents the physical prototyping and implementation of the robotic assembly process. The fabrication process uses a cooperative assembly technique in which robots alternate between placement and support to first build a stable central arch. Subsequently, the construction is continued individually by the robots - building out from the central arch following an interlocking herringbone brick sequence. This methodology is implemented in a full-scale vault (3.6m x 6.5m x 2.2m) structure consisting of 338 glass bricks, built using two large-scale industrial robotic arms.
Sessions chaired by Tomohiro Tachi & Caitlin Mueller, Thursday April 29, 2021
The Canopy Pavilion: A lightweight shading structure using a deployable auxetic linkage membrane – Isvoranu et al
Authors
F. Isvoranu, T. Chen, E. Bouleau, A. Blanc, D. Dietz, M. Pauly
Abstract
We present the Canopy Pavilion, a lightweight shading structure for a social gathering space. The shading surface is realized as a tensioned auxetic linkage membrane, composed of two double-curved anticlastic layers separated by a compression pole. The membrane is assembled flat on the ground from laser-cut hexagonal aluminium panels, and is subsequently mounted on a circular support frame. Tensioning then deploys the surface to its desired target shape. We apply numerical optimization to form-find the equilibrium shape of the tensioned membrane. The geometry of each individual linkage panel is further adapted to reduce material usage, while maximizing the main function of the structure, to provide shading. Our material system offers a number of distinct advantages. Individual panels can be cut from standard sheet material, all connections between panels are identical, the surfaces can be assembled on the ground and deployed easily to their double-curved shape. The pavilion is a first demonstrator for a novel lightweight construction system at architectural scale that has potential applications in facades, roofs, or support structures.
Space Shingles: Casting bespoke connectors for structural shingles – Becker et al
Authors
M. Becker, A. Fromm, P. Mecke, F. Keller
Abstract
The paper describes how established manufacturing methods and certified materials in metal casting are used in conjunction with 3D-printed moulds for creating geometrically complex structural aluminium connectors. To show the potential of this process we propose a novel connector that differs from bespoke tube connectors and traditional spider fittings. We showcase a connector for joining sheet material to form larger double-layered structural assemblies such as decks and shells without the need of any substructure.
The work lays out the digital process chain including design, engineering, and fabrication. This includes topology optimization of connectors towards structure, material use, and casting limitations. It describes the production of individually shaped connectors, which are produced indirectly using a large format binder-jet 3D-sand-printer for casting metal cores. It results in bespoke cast metal connectors with approved material properties. The work is situated between 3D-metal printing and 3D-printing sand moulds for bespoke metal casting.
A possible novel design application of such a plate connector is demonstrated in a shingled double-layered structure. It would allow for a loose-fit overlapping panel detail and thus eliminate elaborate flank machining. Such varying overlap between panels with relatively large tolerances also opens the possibility for constructing nonstandard forms out of standard panels. It also allows to design with reused plates or production-waste material by employing combinatorial methods.
Papers selected for short presentations
Sessions chaired by Tomohiro Tachi & Caitlin Mueller, Thursday April 29, 2021
Double-Curved Spin-Valence Geometric and Computational Basis – Baker et al
Authors
M. Ramirez, E. Baker, E. Harriss, G. Herning
Abstract
This paper describes the geometric and computational basis for creating doublecurved space frame configurations from the Spin-Valence deployable kirigami construction system. The goal was to produce space frames that match non-flat target surfaces to be cut from flat parts and deployed into form.
The Spin-Valence system can be geometrically described as two offset surfaces created from tiled units—the primary surface, which can be seen as the original flat sheet of material, and the secondary surface, which emerges from the primary through spin-folds and reconnections between neighbouring unit hubs. The surfaces are offset from each other and connected through triangulating legs inherent in the cut patterns, thus producing a rigid structural configuration.
The construction must take into account the curvature and non-trivial depth of the space frame, as well as the geometric deployment constraints of Spin-Valence units. The frame is created in two stages. From an arbitrary curved target surface, a planar and conical quad mesh is produced, giving the proposed configuration for the more constrained secondary surface. Each unique unit has a specific deployment space, which is applied to the secondary surface tiles in order to compute a primary surface configuration and inherent triangulating legs, completing the space frame geometry.
dForms with Constant Discrete Gaussian Curvature – Leduc et al
Authors
N. Leduc, C.Douthe, B. Vaudeville, S. Aubry, K. Leempoels, L. Hauswirth, O. Baverel
Abstract
This paper proposes to extend the notions of mean and Gaussian curvatures of smooth and discrete surfaces to semi-discrete surfaces. This class of surfaces, also called piecewise developable surfaces is characterized by a zero Gaussian curvature everywhere except for seams between two patches and vertices. The study focuses on families of surfaces with constant Gaussian curvature along the seams. As a case study of the problem, dForms, closed piecewise developable surfaces formed by two discs of different shapes but equal perimeters, are chosen.
After a topological description of the semi-discrete surfaces, based on the Gauss- Bonnet theorem, two types of dForms with constant Gaussian curvature are studied. The first type describes a two-parameter family based on symmetrical cutting patterns. The symmetry property allows the three-dimensional geometry of this subclass of dForms to be fully described. The second type is asymmetrical and makes use of the properties of the evolute of the curves of the cutting patterns to fulfil the closure condition. In this case, we also propose a method to explore the space of possible configurations using an augmented isometric flow method.
Structural Morphology of Polyhedral Spatial Trusses in Static Equilibrium via 4-polytopic Stress Functions – Konstantatou et al
Authors
M. Konstantatou, M. Akbarzadeh, A. McRobie
Abstract
Graphic statics, a 19th century methodology for the design and analysis of trusses in static equilibrium, has re-emerged recently as a comprehensive framework for designing and analyzing materially efficient structures. Specifically, computational frameworks have been introduced for the structural morphogenesis of compression-only 3D polyhedral trusses by Akbarzadeh et al. (2015). Moreover, the fundamental relation between tension-and-compression 3D trusses in static equilibrium and 4D stress functions has been showed in McRobie (2016). Furthermore, a direct mathematical construction for generating pairs of reciprocal 4D stress functions, and by projection pairs of reciprocal 3D form and force diagrams, has been discussed in Konstantatou et al. (2018). The central role of stress functions in structural morphogenesis was already known by Maxwell (1864a) who used projections of polyhedral (Airy) stress functions to derive 2D trusses in static equilibrium while obtaining design and analysis freedoms. In this paper we apply these constructions to their higher-dimensional equivalents and show how structural morphogenesis of 3D polyhedral, trusses can also have as a starting point 4D stress functions of the form space. The presented direct method has a generative aspect where an underlying grammar can produce a wide range of typologies and can be applied to compression-and-tension cases.
Using Graph Neural Networks to Approximate Mechanical Response on 3D Lattice Structures – Ross et al
Authors
E. Ross, D. Hambleton
Abstract
The promise of computer aided manufacturing (CAM) is to make materializable structures that could not be fabricated using traditional methods. An example is 3D lattices, which may be arbitrarily complex. Variation in the lattice geometry and print media can define a vast spectrum of resulting material behaviour, ranging from fully flexible forms to completely stiff examples with high strength. Panetta et al. (2015) outline a methodology to generate lattice geometries with specified material properties. However, their method relies heavily on finite element analysis of beam models to determine the material properties of a discretely sampled space of lattices. In the present study, we use machine learning to perform a stiffness analysis on highly symmetric lattice geometries with periodic boundary conditions. We train a graph convolutional network on a dataset of lattices sampled continuously from the space of all lattices, then use the trained model to predict deflections for previously unseen lattices. With this approach we are able to approximate the material behaviour of the vast space of all lattice geometries, which offers potential for real-time material feedback at the design stage. It also offers a method to explore a space of building components that are materially sparse yet offer high strength and stiffness. The symmetry of the lattice geometry together with the stiffness analysis creates a homogenized material model, which can be applied to different designs to obtain similar material performance. We illustrate the approach with several examples across different scales.
Sessions chaired by Olivier Baverel, Thursday April 29, 2021
Structural Up-cycling: Matching Digital and Natural Geometry – Amtsberg et al
Authors
F. Amtsberg, Y. Huang, D. Marshall, K. Gata and C. Mueller
Abstract
This paper presents a design-to-fabrication workflow for spatial structures that make best use of a given stock of tree forks. Still little explored, the reuse of structural components beyond their traditional life cycle has the potential to significantly reduce the environmental impact of building structures. While previous work employs complex machining processes to harness the natural variation of tree forks, this work presents a new approach to optimize the use of resourced tree forks as load-bearing joints and find a matching between the intended geometry and naturally available inventory. This approach minimizes extra machine processing time by taking advantage of the structural potential of each individual tree fork that originates from its natural geometry and internal grain structure. The contributions of this paper include: (1) a digital approach for material library intake and management; (2) a geometric matching algorithm to match designed geometry and material library; (3) the development of a structural node geometry that facilitates an efficient automated fabrication process. A human-scale built prototype is presented to showcase the effectiveness of the proposed workflow, demonstrating its potential to be deployed in a practical architectural scale.
Grammars of Interlocking SL Blocks – Shih
Authors
S-G. Shih
Abstract
Grammar is a kind of abstract representations for defining how the composite whole can be derived from a hierarchy of mutually related parts. This paper discusses how grammars can be used as a means to assist the design and construction of large and complex compositions out of a simple building block.
An SL block is an octocube designed for making semi-interlocking structures extensible in three orthogonal directions. String re-write grammars are used to define languages of SL block compositions. It is expected to establish a mathematical basis for SL block compositions. Investigations and speculations through concepts, principles and notations of such a grammatical approach are proposed. A building frame form generator is devised to provide views towards how SL blocks can be systematically arranged to create architectural forms. With the grammatical approach, it might be possible to implement compilers for high level composition languages of SL block compositions.
Corrugated Cardboard Shell: A pavilion project of an architectural workshop – Vestarte et al
Authors
L. Vestarte, P. Vestartas, R. Kucinskas
Abstract
This paper presents mesh-discretisation and assembly methods for quad-based shellstructure. The study case is a corrugated cardboard shell 3m in height and spans up to 6m in diameter and is supported at 5 arbitrary points. The structure was built from-two layer 3mm corrugated cardboard sheets, consisting of 391 sets of planar quadrilateral elements (1537 total count of unique pieces). Since the principal fabrication constraint was a 2-axis laser cutter, the approximation of cutting angle for finger-joints was required. The laser cutter, with the maximum bounding area of 600 x 900 mm, also restricted the size of the panels, while the directionality of corrugated material posed constraints on geometrical proportions of the panels and their orientation within the cutting sheet. The shell was assembled without using heavy scaffolding or any adhesives, thus relying on material strength and friction provided by the connection method. The assembly sequence and insertion vector had a crucial role in the act of such construction. The pavilion was assembled within less than 12 hours, including the time spent for sorting the unique pieces.